- Reaction score
- 10,404
- Points
- 1,160
I thought bringing these references into one place might be interesting.
The program intent seems to be to create a truck that combines the M270/HIMARS with NASAMs and/or Patriot with Tomahawk. The desire is for an autonomous or optionally manned vehicle that will fit in the back of a C-130 while carrying two pods of missiles.
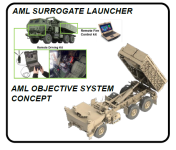
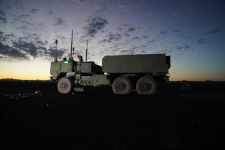
thedefensepost.com
www.twz.com
www.army.mil
www.lockheedmartin.com
breakingdefense.com
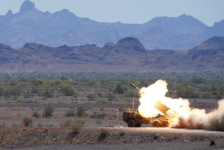
The program intent seems to be to create a truck that combines the M270/HIMARS with NASAMs and/or Patriot with Tomahawk. The desire is for an autonomous or optionally manned vehicle that will fit in the back of a C-130 while carrying two pods of missiles.
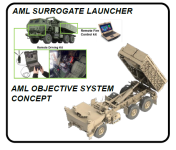
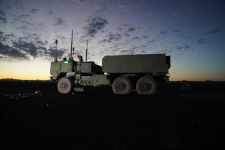
AUTONOMOUS MULTI-DOMAIN LAUNCHER (AML)
AML is a Long Range Precision Fires Cross Function Team, DEVCOM Aviation & Missile Center, and DEVCOM Ground Vehicle Systems Center Science and Technology initiative to develop and demonstrate an autonomous, unmanned, highly mobile, C-130 transportable launcher. The prototype launcher will be capable of leader-follower autonomy, autonomous way point navigation, drive-by-wire, and remote launcher turret and fire control operation. It will be capable of launching longer munitions while remaining compatible with the current munitions.
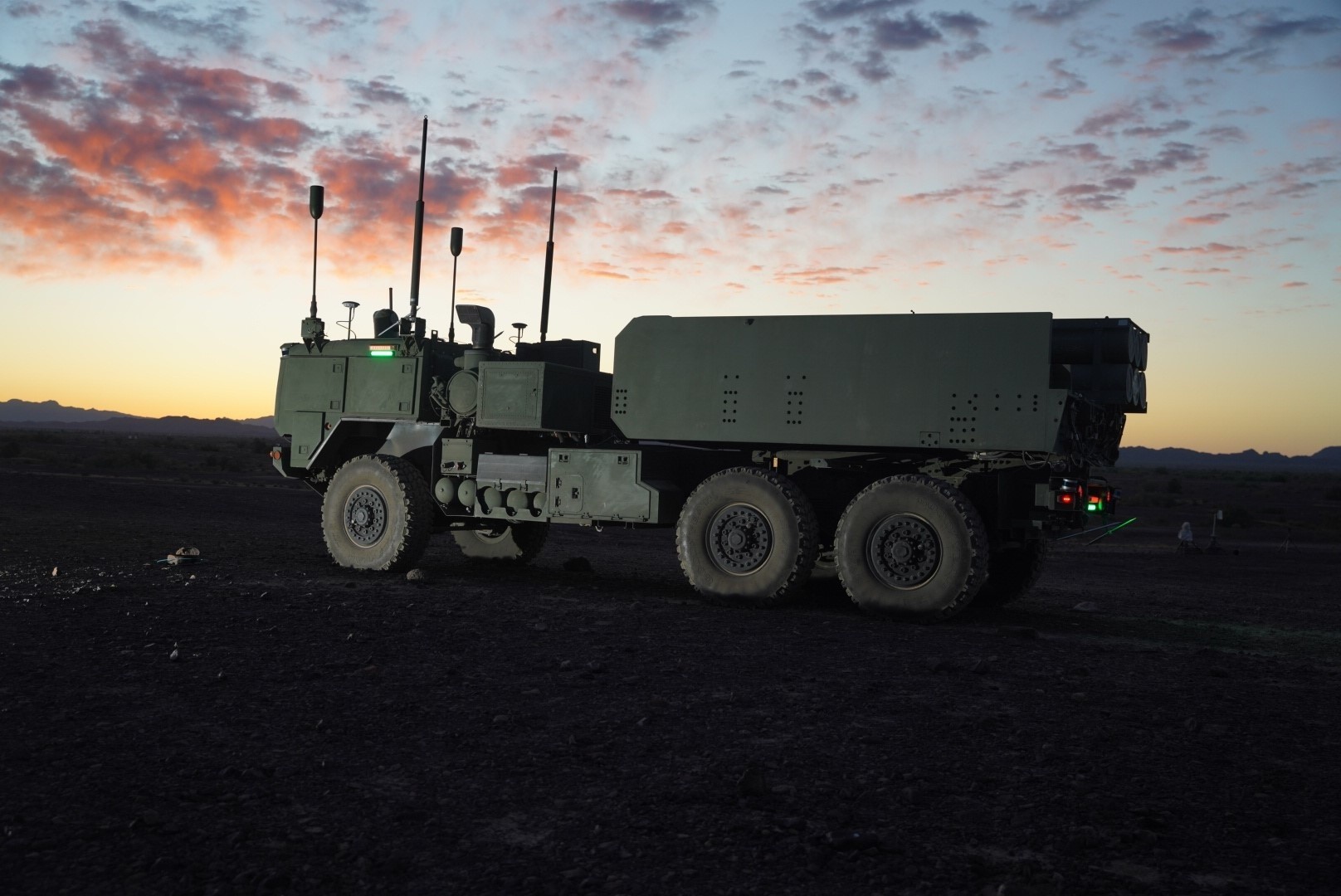
US Army Demos Unmanned HIMARS
The US Army demonstrated the Autonomous Multi-Domain Launcher, which offers increased firepower without the risk of human casualties.


Our First Look At The Army's Unmanned HIMARS Launcher Truck Firing
The Army sees the the Autonomous Multi-domain Launcher (AML) as an important way to increase firepower, but not personnel demands.

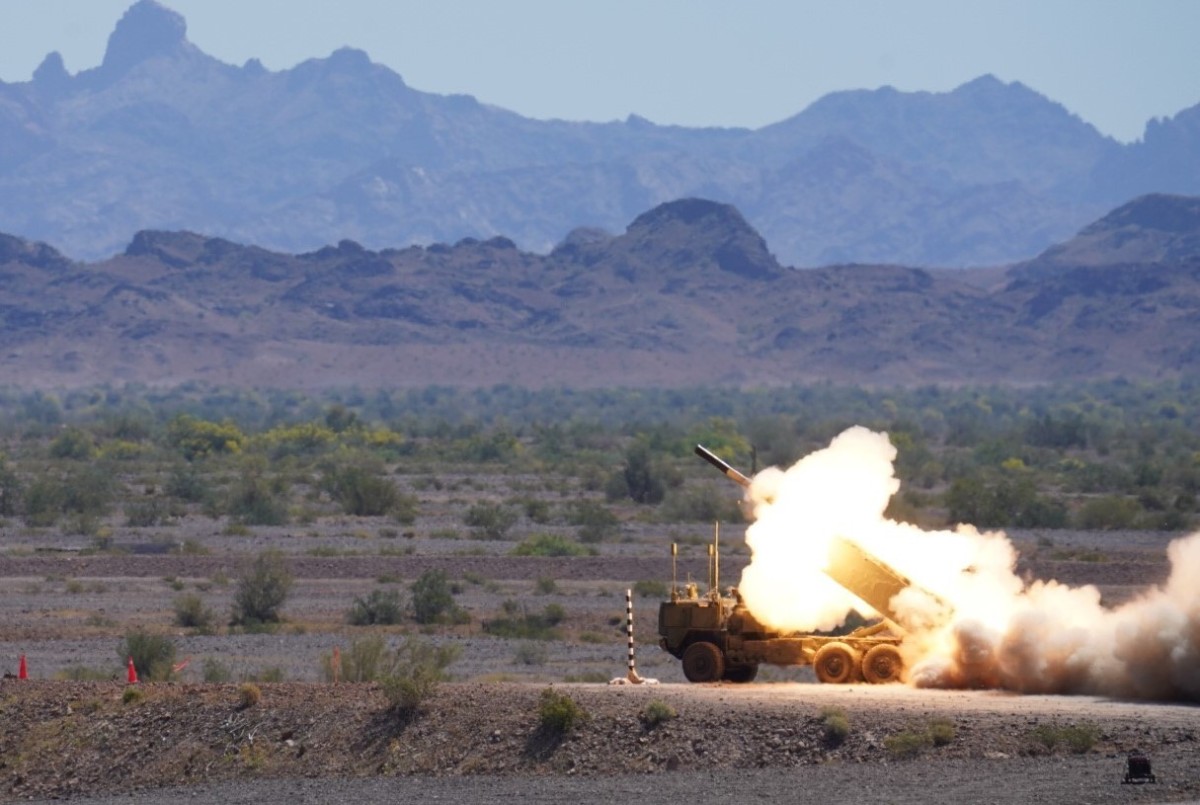
Autonomous Multi-domain Launcher meets another program milestone
REDSTONE ARSENAL, Ala. — Mission success. Another pivotal stride was made by the Autonomous Multi-domain Launcher as the combined team of the U.S. Army...


Autonomous Solutions: Lockheed Martin Advances Uncrewed Capability for Combat-Proven HIMARS
Lockheed Martin has successfully demonstrated uncrewed capability with a surrogate HIMARS® launcher, a significant milestone in the development of autonomous systems that can operate collaboratively with manned vehicles.
During its time at YPG, the AML launched three RRPRs in a successive ripple fire mission. In all, six RRPRs were successfully fired from the AML in a demonstration of the launcher’s ability to maneuver under supervised autonomy from a hide location to a firing point, turn to an assigned heading and execute fire control commands from a remote gunner position.
Over the past week leading up to the initial live fire, the AML successfully demonstrated each of its mobility modes: tele-op, waypoint navigation and convoy operations.
Soldiers from the Tennessee Army National Guard 1-181st Field Artillery Regiment were also on hand to train on and operate the AML.
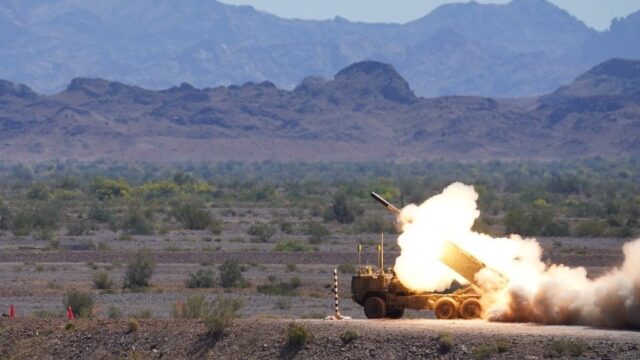
Army unveils plans to acquire two different sizes of autonomous launchers - Breaking Defense
The heavy variant would be based on a Palletized Loading System and fire either Tomahawk or PAC-3 missiles, while the medium-class launcher would use an FMTV to fire Multiple Launch Rocket System munitions or AIM-9X interceptors.

The US Army is interested in acquiring two new autonomous platforms under a new initiative it’s calling the Common Autonomous Multi-Domain Launcher (CAML).
“CAML is an autonomous/optionally crewed, highly mobile, air transportable, cross domain fires launcher with the potential to augment or replace existing Army launchers,” the service said.
As for the smaller, CAML-M variant, the service is interested in using a Family of Medium Tactical Vehicle (FMTV) as the base to launch Multiple Launch Rocket System (MLRS) Family of Munitions or the new Indirect Fire Protection Capability (IFPC) with AIM-9X interceptors.
For the CAML-H variant, the Army wants to integrate a launcher onto a M1075 Palletized Loading System tactical vehicle — or similar 15-ton class chassis — that can then fire the Tomahawk Land Attack Missile or the Patriot Advanced Capabilities Three (PAC-3) Missile Segment Enhancement interceptor. However, the service did not specify how many rounds each launcher should be able to hold.
“The CAML-M will be supported by an Autonomous Resupply Vehicle (ARV) capable of autonomously reloading pods/cannisters of missiles onto the CAML-M with minimal to no human intervention,” the service explained.
“The CAML-H variant will be an Autonomous Self Resupplying System capable of autonomously reloading cannisters of missiles onto the CAML-H with minimal to no human intervention,” the Army added.
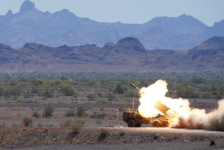